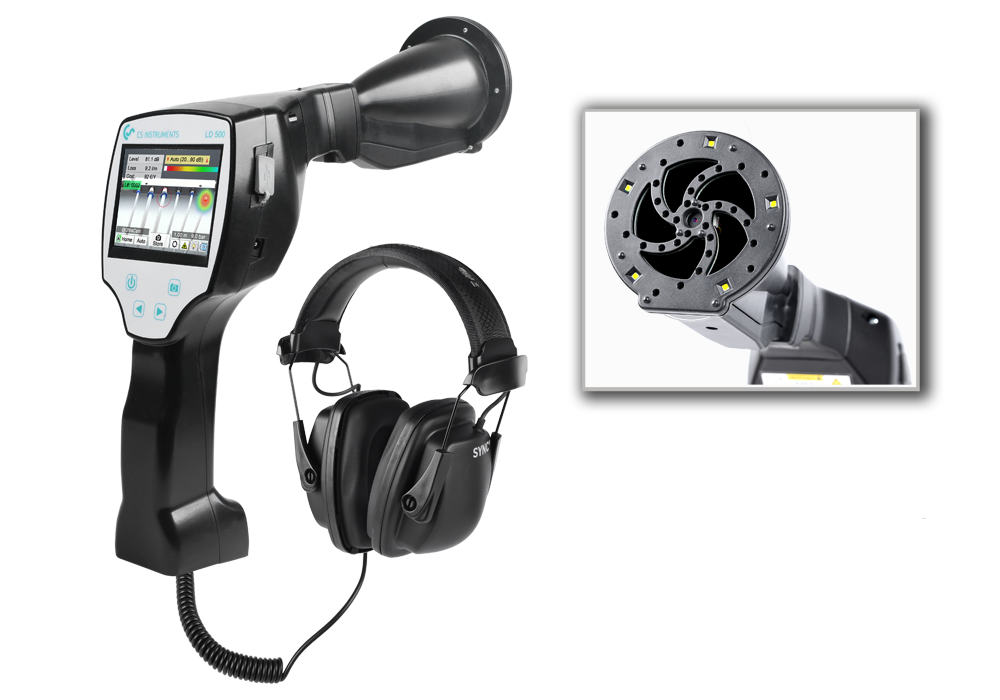
Kamera ultradźwiękowa UltraCam LD 500/510
wykorzystuje 30 mikrofonów MEMS do obliczania i wizualizacji obrazu ultradźwiękowego. Urządzenie sprawia również, że niesłyszalne ultradźwięki stają się słyszalne.
W krajach uprzemysłowionych około 10% całkowitego zużycia energii elektrycznej w przemyśle jest wykorzystywane do wytwarzania sprężonego powietrza, w Niemczech jest to aż 14%. Nieszczelności są głównym czynnikiem strat energii, a większość systemów sprężonego powietrza ma straty w zakresie od około 20% do 40%, a w słabych systemach nawet ponad 60%. Eliminacja wycieków sprężonego powietrza jest najskuteczniejszym sposobem na zmniejszenie zużycia energii. Wycieki sprężonego powietrza często marnują 8760 godzin (24 h x 365 d) energii rocznie i wydłużają czas pracy sprężarki, co również skraca okresy między konserwacjami. Dlatego konieczne jest regularne wykrywanie i eliminowanie nieszczelności. Nasza seria LD oferuje wszystkie funkcje potrzebne do wykrywania wycieków i mierzenia konsekwencji w postaci zużycia energii i zmarnowanych pieniędzy.
Wysokie wskaźniki wycieków sprężonego powietrza i nieprawidłowo zaprojektowane komponenty (sprężarki i zbiorniki sprężonego powietrza) zmniejszają wydajność systemu sprężonego powietrza, generują niepotrzebneemisje CO2, a także zmniejszają konkurencyjność. To, ile sprężonego powietrza potrzeba do produkcji w ciągu tygodnia i jak należy zwymiarować komponenty, aby działały jak najwydajniej i były wykorzystywane w pełni, można bardzo łatwo i niezawodnie zmierzyć za pomocą czujnika przepływu. Na przedstawionym wykresie można zobaczyć profil przepływu zmierzony za zbiornikiem sprężonego powietrza w firmie farmaceutycznej w RPA przez około 10 dni.
Zielona krzywa odpowiada rzeczywistemu zmierzonemu profilowi przepływu objętościowego (średnia ruchoma), a czerwona krzywa profilowi przepływu objętościowego po "symulowanej" eliminacji wycieku. Jak widać, krzywa przesuwa się w dół. W okresach zaznaczonych na czerwono produkcja była zatrzymana i nie produkowano żadnych towarów - innymi słowy, sprężone powietrze uciekało w tym czasie tylko przez nieszczelności i otwarte dysze. Oczywiście wartość ta powinna być zawsze jak najniższa i powinna znacznie spaść po wyeliminowaniu wycieków lub innych optymalizacji zużycia. Opierając się na następujących założonych wartościach dla systemu, istnieje potencjał do poprawy, co można zobaczyć w poniższej tabeli.
Jednostka | Pomiar przed rektyfikacją | Pomiar po korekcie | Ulepszenia |
Średni przepływ objętościowy[m3/h] | 500 m³/h | 250 m³/h | 250 m³/h |
Przepływ objętościowy bez produkcji[m3/h] | 316 m³/h | 66 m³/h | 250 m³/h |
Wskaźnik wycieku [%] | 63,2% | 26,4 % | 36,8 % |
Potencjał oszczędności [€ / a] | 75.840 € / a | 15.840 € / a | 60.000 €/a |
Emisja CO2 | 127,41 ton / rok | 26,61 ton / rok | 100,8 ton / rok |
Poniższy wykres przedstawia profil przepływu objętościowego w piekarni, która produkuje w następujących warunkach:
Termiczny czujnik przepływu VA 500 został zainstalowany za zbiornikiem sprężonego powietrza w celu pomiaru zużycia w obu halach. Na poniższym wykresie oryginalny profil przepływu objętościowego (jasnozielony) pokazuje włączanie i wyłączanie sprężarki. Dla lepszej porównywalności obliczono i wykreślono również średnią ruchomą (ciemnozielony). Na tej podstawie można wyciągnąć następujące wnioski: Pomimo braku produkcji przed godziną 10:00, sprężarka dostarcza dużo sprężonego powietrza. Rzeczywiste "szczyty produkcyjne" są bardzo małe w porównaniu do obciążenia podstawowego. Wskazuje to na bardzo wysoki wskaźnik wycieków. Aby potwierdzić to założenie, zawory kulowe do maszyn w obszarze wyłączenia (w hali 1) zostały zamknięte, aby ich nieszczelności nie były już zasilane sprężonym powietrzem. Większość nieszczelności znajduje się zwykle w maszynach i wokół nich. Późniejszy stały spadek poziomu profilu przepływu objętościowego pokazuje, że podstawowe obciążenie można znacznie zmniejszyć od zamkniętego zaworu kulowego do zaworu kulowego. Wskazuje to na wpływ naprawy nieszczelności na profil sprężonego powietrza w tej piekarni.
Jeśli maszyny w hali 1 zostaną ponownie uruchomione, zawory kulowe muszą zostać otwarte, a sprężone powietrze ponownie wydostaje się przez nieszczelności.
Opisany tutaj proces powinien być przeprowadzany w firmie cyklicznie, aby utrzymać wskaźnik wycieków na jak najniższym poziomie w perspektywie długoterminowej. Celem działań powinno być osiągnięcie stałego wskaźnika wycieków na poziomie 5-10%, ponieważ doświadczenie pokazuje, że jednorazowe poszukiwanie i naprawa nie zmniejsza trwale wskaźnika wycieków, a nowe wycieki naturalnie pojawią się później.
Praktyczna wskazówka: Aby nie przegapić optymalnego czasu na audyt szczelności, zaleca się użycie czujnika przepływu (np. VA 500) w głównej rurze za zbiornikiem. Zaleca się, aby okres pomiaru wynosił co najmniej jeden tydzień (od poniedziałku do niedzieli). Ponadto pomiar przepływu objętościowego może być wykorzystany do walidacji wyników wyszukiwania i usuwania wycieków, ponieważ musi to zmniejszyć przepływ objętościowy podczas postoju.