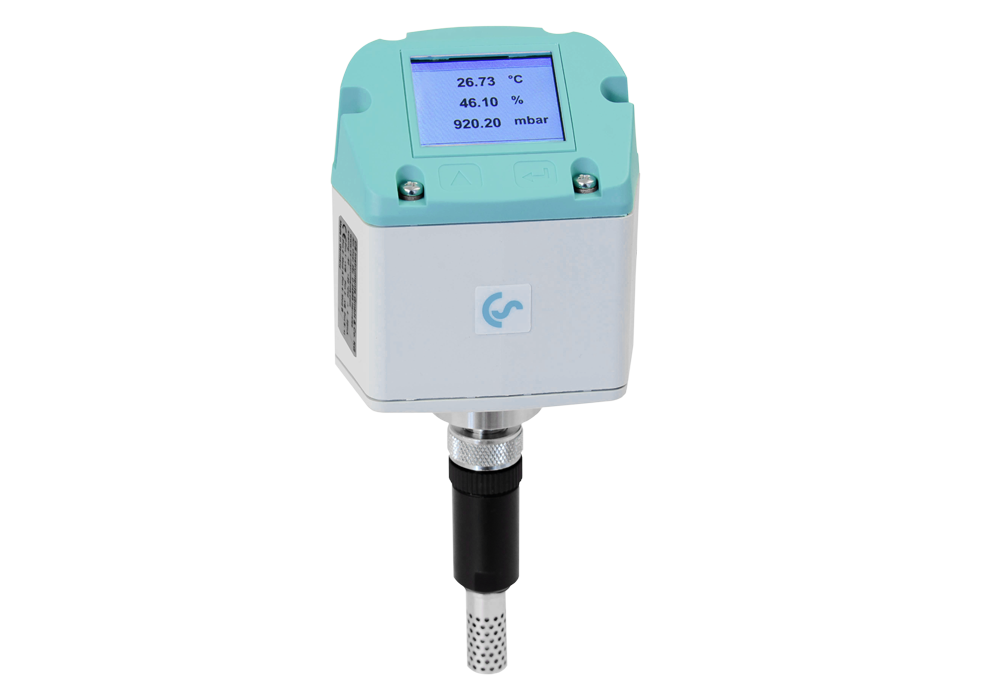
IAC 500 sensor for measuring ambient conditions
(absolute pressure, temperature, rel. humidity), incl. wall bracket
Step 1
First minimize the compressed air demand caused by production and Leakages. Then you can precisely measure the actual demand for production.
Choice of automation technology: use of electric motors vs. pneumatics
Conclusion:
Electric drives are more efficient for movements, but up to 22 times more energy-intensive than pneumatics for holding tasks. The selection should be based on the total costs, which are made up of acquisition and ongoing Energy consumption. The combination of both automation technologies is often the most energy-efficient.
Eliminate Leakages:
Compressed air leaks cause significant economic and environmental damage. The escaping, purified Compressed air increases operating costs and CO2 emissions, with large Leakages accounting for the majority of costs despite their rarity. While Robust stainless steel pipes rarely leak, most Leakages occur in production, especially on machines and their connecting elements. Ultrasonic Leak detectors and acoustic cameras can locate Leakages both acoustically and visually.
Step 2
With a clearly defined requirement, production and treatment can then be optimized in terms of energy. This ensures that Compressors and treatment are efficiently designed to meet the actual, minimized demand.
Would you like to know how you can monitor the specific performance of your compressed air system? This article gives you detailed insights: click here. If the specific performance of your system does not meet your expectations, there are effective measures to optimize Compressed air generation and treatment.
Intake conditions:
Temperature, Humidity, Ventilation and Absolute Pressure in particular play a crucial role in the Efficiency of Compressed air generation. High temperatures can increase operating costs, while inadequate ventilation can reduce efficiency even under optimal conditions.
Compressor control:
Different types of Compressors each have their own advantages and disadvantages in terms of Efficiency, Maintenance and Cost. An optimal setup could consist of one variable-speed Compressor for peak consumption and two base-load capable Compressors. A speed-controlled Compressor adjusts its motor speed variably to the air demand and is particularly efficient at a load of between 40 % and 80 %. This combination not only achieves high efficiency and a uniform operating pressure, but also creates important redundancy. In the event of a Compressor failure, this redundancy prevents a possible and expensive production stop, as the other Compressors can continue to cover the air demand.
Heat recovery: Effective heat recovery increases the efficiency of a compressed air system by utilizing the waste heat generated during compression, effectively reducing the operating costs of the compressed air system.
System age, condition and maintenance:
Older systems are usually less efficient than newer Compressedair systems. If they are not in optimum condition, this can have a negative impact on operation and thus Energy efficiency, leading to unnecessary costs. In general, regardless of age, regular maintenance and inspection is essential to maintain the Efficiency of the system and identify potential problems at an early stage.
Optimizing the pressure level / minimizing pressure losses:
A higher pressure level often leads to increased operating costs. For example, an increase in pressure of just 1 bar can increase Energy consumption by 5 to 7 percent. It is advisable to operate the system pressure only as high as is necessary for the smooth operation of the system. Pressure losses in the distribution network, for example caused by saturated filters or other factors such as Leakages or inadequate line dimensioning, create the need for an increased pressure level at the Compressor. Regularly checking and adjusting the system can therefore help to maintain the most efficient operating pressure and save energy costs.
Optimize compressed air tanks and Circular pipelines:
The use of compressed air tanks and Circular pipelines can be used to stabilize pressure by ensuring even air distribution. If the line diameter is too small, this can lead to high flow rates and increased pressure losses. The correct dimensioning of the lines and compressed air tanks is all the more crucial for the efficiency of the compressed air system.
Observe compressed air treatment in accordance with ISO 8573-1:
Adequate compressed air drying and compressed air filtration can entail additional energy costs, but is often an essential measure to ensure the air quality required for certain production processes. The requirements in this area are particularly high in industries such as the food industry, medical technology and pharmaceuticals, as the compressed air often comes into direct contact with end products. It is therefore essential to monitor the Compressed air quality regularly. Otherwise, risks can arise that could damage machines or render product batches unusable due to contamination. Constant monitoring to maintain the balance between costs and required purity should be the focus to ensure both Efficiency and safety of the system.
The use of a Desiccant dryer for high drying requirements:
If very dry compressed air (< - 40 degrees Dew point) is required, the use of an Desiccant dryer within the compressed air system is recommended. There are the following differences:
You can't optimize what you don't measure.
Sensors are essential for the Energy efficiency and optimization of compressed air systems. They enable the monitoring and diagnosis of system components in order to detect inefficiencies and anomalies at an early stage. A sensor-based approach ensures maximum Efficiency, cost savings and a sustainable use of resources. It is a crucial step in uncovering potential for improvement and implementing well-founded optimization measures.